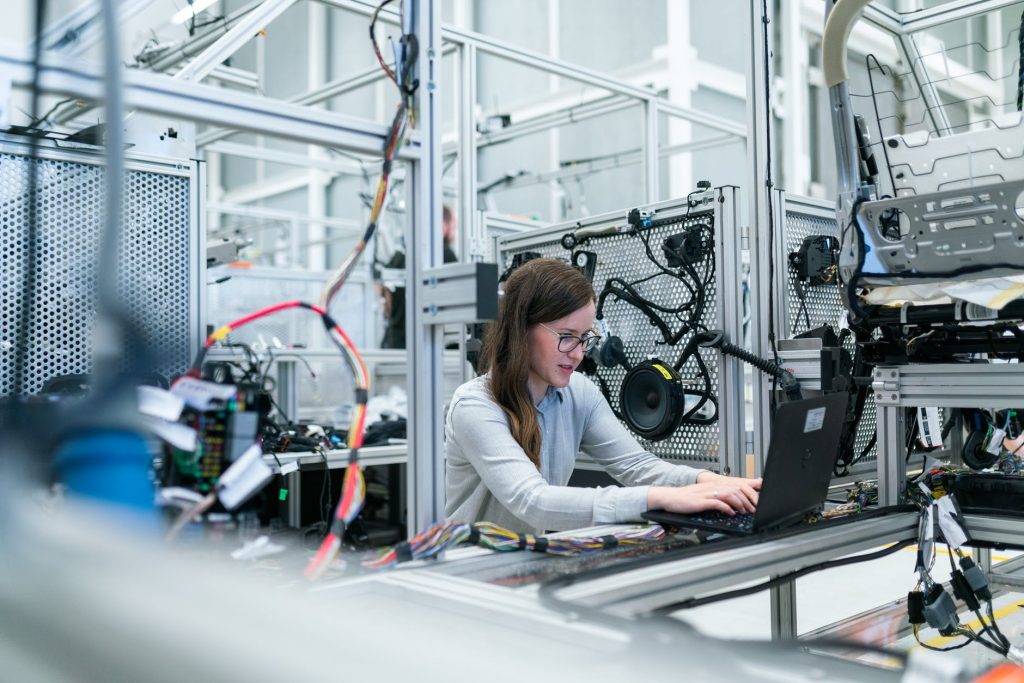
Machine learning operations data analytics and asset health monitoring engineers can improve plant or company operations and lessen the need for dependability. It is essential to utilize preventative maintenance programs to ensure steady operations, ensure conformity to warranty requirements, and take care of issues that may affect production – before they occur.
Types of Industrial Machine Preventive Maintenance
There are four primary categories of preventative maintenance to select from. While they’re all organized and scheduled differently, they’re all designed in the spirit of planning maintenance. This is because different companies’ processes require different types of maintenance.
Preventive Maintenance Based on Use
The usage of an asset triggers the need for usage-based preventative maintenance to be conducted on it. A date for upcoming maintenance or inspection can be determined with the aid of this type of maintenance, taking into account the typical everyday usage of an asset and its exposure to the surrounding environmental conditions.
Calendar- Or Time-Based Preventive Maintenance
When using a time- and calendar-based approach, preventive maintenance is carried out according to intervals that have been scheduled and in intervals established with calendars. Maintenance is initiated when the date of the request approaches and the needed work instructions have been issued.
Predictive Maintenance
The aim of predictive maintenance would be to set up the corrective maintenance procedure in advance, before any malfunction has ever occurred. Before the team can even begin to estimate when maintenance needs to be carried out, they need to first assess the condition of the equipment or machine. Following that, maintenance chores are scheduled in order to prevent unanticipated breakdowns of equipment.
Prescriptive Maintenance
Preventative maintenance does not only tell when a failure is likely to occur; however, it also reveals the reason for the failure to appear. This type of maintenance allows you to evaluate and choose the most suitable options and possible outcomes to minimize the chance of damaging impacts to the process that could occur.
Reactive Maintenance
It is also known as “breakdown maintenance,” it’s a method where the focus is focused on the repair or replacement of equipment and restoring it to its original state only when it has already failed or was deemed as inoperable. In essence, reactive maintenance is the process of addressing a problem or issue only after it’s already happened, without taking any preventative precautions. This maintenance can still be performed, but it’s suggested only for easy to replace, inexpensive components that are a failure will not cause collateral damage or which cost less as preventative care.
Preventive vs. Predictive Maintenance Verdict
“Preventive maintenance” comprises a wide range of actions and duties. Each system’s manufacturing component needs regular cleaning and lubrication. In some cases, an extensive maintenance program may be required to repair, there are only two locations to go, either to recondition or replace part. If parts are not readily available, storage is needed especially for large machineries so you may search “warehouse for rent” for storage needs.
Predictive maintenance, on the other hand, is an upgrade to preventative. Both sorts of maintenance prevent mechanical problems. Predictive maintenance can go further and is more accurate but requires more information. The model’s predicted lifespan and performance history are taken into account. Predictive models for maintenance can provide precise forecasts of system faults with more data.